StrAU
Structural subdivisions of Aerospace Propulsion Institute (AerPI)
taking part in StrAU
Seven departments: “Automatic Systems of Power Plant”, “Engineering drawing”, “Construction and Design of Aircraft Engines”, “Aircraft Engines Theory”, “Thermal engineering and heat engines”, “Engine Production Technology”, “Ecology and life safety”.
Two institutes: “Innovative Production Technologies Institute”, “Machines Acoustics Science and Research Institute”.
Nine research laboratories: “Aeronautical Products Vibration Strength and Reliability Industrial Research Laboratory”, “Mechanical and Spot Blasting Materials Treatment Industrial Research Laboratory”, “Manufacturing Processes Automation Technologies Industrial Research laboratory”, “Laboratory of additive technologies”, “Laboratory of energy-efficient and energy-saving technologies”, “Jet Engine Workflows laboratory”, “Rapid prototyping laboratory”, ‘Thermal Power Engineering laboratory’.
Six scientific and educational centers: “Vibroacoustics of Machines”, “Laser systems and technologies”, “Mechatronic Systems and Robotic Complexes”, “Gas-dynamics research”, “Energy efficiency”, “Prototyping”.
Two multiple access centers: “Interdepartmental Training Research and Production Center СAM-technology”, Teaching and Research Production Center Vibration strength and reliability of aerospace parts”.
Three joint scientific subdivisions in cooperation with foreign universities and companies: Russian-German “Advanced engines research institute” (with University of Stuttgart, Germany); Scientific laboratory “Gas-turbine engines rotor dynamics” (with Polytechnic University of Turin, Turin, Italy); Russian-German Scientific laboratory “Tensometry and telemetry” (with MT – Solutions company, Germany); production and technological laboratory "Fundamental research and innovation technology".
Other departments: “Student Design Bureau of aircraft engines”, “Center for History of aircraft engines”.
Educational programs, implemented in StrAU
Direction 13.03.03 “Power engineering”: bachelor’s degree program “Accessory and power plants control systems” with the number of students – 84 people;
Direction 15.03.04 “Automation of technological processes and production”: bachelor’s degree program “Mechatronic and robotic systems” with the number of students – 71 people;
Direction 15.03.05 “Design and technological support of machine-building manufacture” of bachelor’s degree programs:
- “Innovative production technology” with the number of students – 73 people;
- “Engine manufacturing technology” – personnel contract training for JSC “KUZNETSOV” with the number of students – 75 people;
Education of students at JSC “KUZNETSOV” was organized in 2000 to effectively solve stuffing problems of the leading aerospace company. A unique system of training and manufacturing processes integration was developed. Students work and study in the factory and perform laboratory works at the university. Coursework and thesis are carried out on topics, which are formed in the factory departments under the joint leaderships of a university teacher and a specialist from JSC “KUZNETSOV”.
Direction 24.03.05 “Aircraft engines” of bachelor’s degree programs:
- “Design of aircraft engines and power plants” with the number of students – 44 people. Russian partners: JSC “KUZNETSOV”, JSC “Metallist”. Their roles are: coordination of curricula, formation of actual topics of the coursework and thesis, students consulting by coursework performing, participation in a defense of the coursework or thesis, realization of industrial practices.
- “Organization and manufacturing management” with the number of students – 53 people.
Specialty 24.05.02 “Design of aircraft and rocket engines”: specialist program “Project management and integrated information technology in aero-engine manufacturing” with the number of students – 71 people. Russian partners: JSC “KUZNETSOV”, JSC “NPO “Saturn”. JSC “Metallist”. Their roles are: coordination of curricula, formation of actual topics of the coursework and thesis, students consulting by coursework performing, thesis guidance, participation in a defense of the coursework or thesis, realization of industrial practices, assignments development for the contract training and active participation in it.
Direction “Aircraft engines” of master’s degree programs:
- “Hi-tech innovative machine-building manufacture” with the number of students – 18 people;
- “Mechatronic pneumohydraulic accessories and systems” with the number of students – 11 people;
- “Integrated information technology in aero-engine manufacturing” with the number of students – 2 people. Russian partners: JSC “KUZNETSOV”, JSC “Metallist”. Their roles are: coordination of curricula, formulation of actual topics of scientific works, students consulting, equipment provision for the experimental work, participation in scientific work defenses, realization of industrial practices.
- “Power plants and energy systems of aircrafts” with the number of students – 1 person. The main partner – Stuttgart University (Germany). The training is carried out in the form of the integrated Russian-German education. 1st year students study at the home university. 2nd year students have an opportunity to study at the partner university to obtain a double diploma. There is also a possibility of students exchange for a semester.
Post-graduate programs (94 people):
05.07.05 Heat and electric rocket engines and power plants of aircrafts; 1.02.06 Dynamics, strength of machines, devices and equipment; 05.07.07 Control and testing of aircrafts and their systems; 24.06.01 Aeronautical and rocket space engineering”; 05.02.22 Manufacturing process management.
Examples of successful career development of graduates
Efimov E.V. has gone the way from the engineer to the chief designer after three years of working in the NPO Saturn Company; Selivanov I.A. has become the head of the strength department after two years in design bureau of JSC “Kuznetsov” Company; Tsygankov I.V. has become the head of the regional division after two years of working in "Kelvion Mashimpeks" (Germany); Zhdanov I.A. and Sokolov M.V. after graduation enrolled in a Doctoral program of the University of Stuttgart (Germany); Klusachek M. has become a leading specialist of the turbocharged division after three years of working in the Scientific and Technical Center of the BOSCH Company (Shtutgart, Germany); Sergeev D.V. – Deputy director of the factory; Ivanova OA - Deputy Head of department of JSC "Russian Railways"; Korchagin I.O. and Valuev S.T. - Department heads of JSC “Kuznetsov” Company; Zhukov D.S. - Deputy head of the department of "Metallist-Samara" Company; Evgeny Suslin, Head of Center of Excellence, ALCOA Artem Korotygin, Project Manager for Polymeric Composite, JSC "NPO "Saturn" and many others.
Main completed StrAU projects in the past three years
1. Integrated project of creation the high-tech manufacturing "Creation of effective design technologies and high-tech manufacturing of high-power gas turbine engines for the ground power plants”. Project Manager – Alexander Ermakov, Director of Aerospace Propulsion Institute SSAU, was born in 1951. Industrial partner – JSC "Kuznetsov". contract value is 190 million rubles.
The original technical solutions for the main engine components have been developed and implemented, reasonable geometric dimensions which provide required reliability and effectiveness of the modified and uprated engines have been chosen by performing the simulations and experiments. As a result of work upgraded compressor has been designed. The optimization of the low pressure turbine and free power turbine workflows was performed considering the mutual influence of turbines, enabling improved efficiency of the turbines. As a result of the works air brake PT-36-32 (32 MW) has been designed with a wide application "virtual" testing technology in the design process, implemented in the software package NUMECA FineTurbo. A technical proposal on the final version of the intermediate-pressure compressor support design with a modified number and shape of racks was found in order to radically reduce the amplitude of dangerous harmonics acting on the impeller of the fifth compressor stage. This proposal has been obtained as the result of the complex "virtual" gas-dynamic and strength tests. 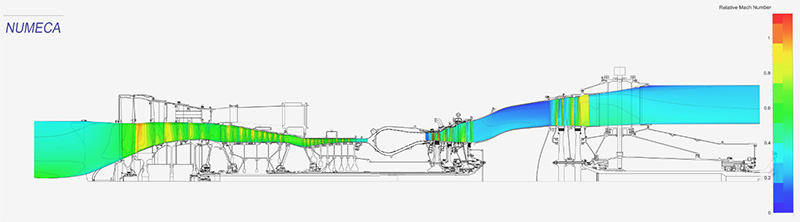
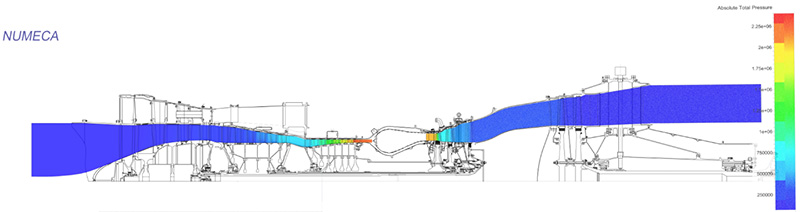
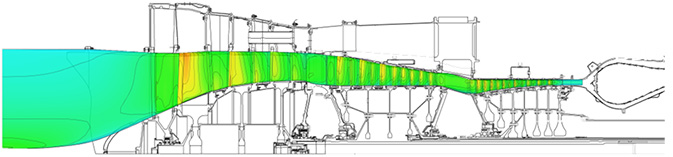
Due to cooperation between SSAU and JSC "Kuznetsov" was made the numerical simulation of the workflow of all Turbomachinery gas turbine engine NK-36СТ. Models were created as separate units (compressors and turbines), and a complex e model of three-stage compressor (low pressure compressor + intermediate-pressure compressor + high pressure compressor), as well as a joint model of four-stage turbine (high pressure turbine + medium turbine pressure + low pressure turbine + free power turbine). Created joint models of compressors and turbines are unique in the world.
Developed and implemented radial-face seals with hydrodynamic and hydrodynamic lubrication, elasto-damping piping supports, vibration isolators made of Metal-Rubber (MR) material. Upgraded unit APM-25, allowing to reduce influence of the steering system units of gas-dynamic stability of compressor and combustion processes in the combustion chamber of the engine NK-36SТ. Developed computerized complex devices for bench control angular and linear displacement element rotating units of gas-turbine engines, namely, measuring the dynamic changes of radial clearances and profile end section of fan blade (PRIZ-1) and measuring a dynamic displacement element (ILDP-8) angular contact bearing high-pressure compressor. It has been created burner for the combustion chamber of the engine NK-36SТ with increased to 32 MW capacity, developed two versions of unified combustion chamber of the engine NK-36SТ, the study of the burner in the experimental tests allowing to choose the best mode of its work with good parameters of emission of Nox and CO.
Produced the experimental technological process of the modified low pressure compressor gas generator (NK-36) rotor blades, developed a set of measures to improve the accuracy control of geometrical parameters of blades and their castles, including during the treatment. Received a wax model of the compressor stator blades and transferred to JSC "Kuznetsov" for the production of castings with directional crystallization. It has been developed The technology of selective laser sintering bladed swirler for the gas turbine engine. As a collaborator in this project has been Russian Research Institute of Aviation Materials. They have done testing of obtaining parts made of alloy VTI-4 and alloy VJL21, which are not inferior to the properties of the alloys-analogues made in the USA.
2. The agreement with the Institute of Biomedical Problems, Russian Academy of Sciences to create a simulator vibration isolation systems for the International Space Station (ISS) together with a stand for the training of astronauts on the ground with simulated space conditions. In April 2015 the space cargo ship "Progress" delivered to the ISS treadmill for Russian cosmonauts to the vibration isolation system, designed and manufactured in Samara State Aerospace University, which allowed the US to remove the track from the Russian segment of the station and in it to date, all domestic production of simulators;
Project Manager - Alexander Ermakov, Director of the Institute of engines and power plants SSAU, born in 1951. The amount of the contract - 10 million rubles. 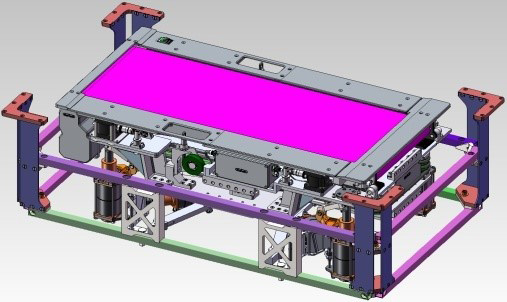
3D model of the simulator "Treadmill" with vibration isolation system
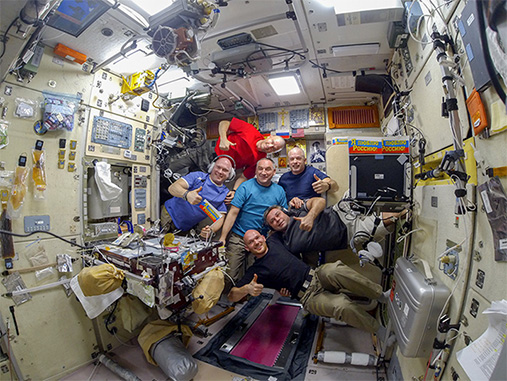
Simulator "Treadmill" on the ISS
3. The agreement with the Federal State Autonomous Educational Institution of Higher Education "Saint Petersburg State Polytechnic University" "Creating parts and aircraft engine components production high-technology methods of heterophase powder metallurgy." .
Project Manager - Sergey Murzin Professor. The amount of the contract - 10.47 million rubles. The results of the research project is a development of technological head shape for the technology implementation of direct laser growing complex-dimensional products from powder alloys; technological development of recommendations for the restoration of worn and / or damaged geometry of metal and aircraft engine production by direct laser deposition.
4. The agreement with JSC "CIC CO." Project Manager - Nikolay Pronichev, deputy head of the department of aircraft engines production SSAU, born in 1950. The amount of the contract - 6.5 million rubles.
In the course of work have been mastered advanced production technology, can reduce the time and improve the quality of R & D, especially at the stage of prototyping and variant studies. Thus, it became possible to provide the Samara region plant, the maximum access to modern engineering and manufacturing complex, integrated environment "design, pre-production, experimental production" in order to improve the quality and competitiveness of products produced by industry in the region.
5. The agreement with with JSC "Kuznetsov" on the preparation of serial production of a number of parts of the engine NK-33. Project Manager - Nikolay Pronichev, deputy head of the department of aircraft engines production SSAU, born in 1950 The amount of the contract - 12 million rubles. Due to the contract for three years innovative manufacturing techniques for unique rocket engine parts have been worked out. It has been done obtaining billets of special parts on the basis of rapid prototyping methods, magnetic-pulse pressing copper jacket cooling of combustion chamber, getting with a complex profile parts made of sheet materials for special blanks by hot volume stamping, drawing special thermal barrier coatings on the surface of the rocket engine combustion chamber.
There is a under development of small gas turbine engine in Institute of engines and power plants SSAU. There are a number of designs developed using a "virtual analog" technology, mastered the technology of important engine parts production.
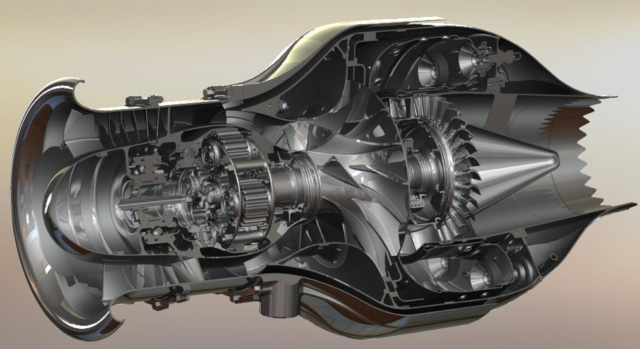
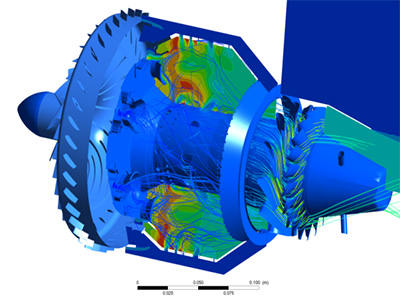
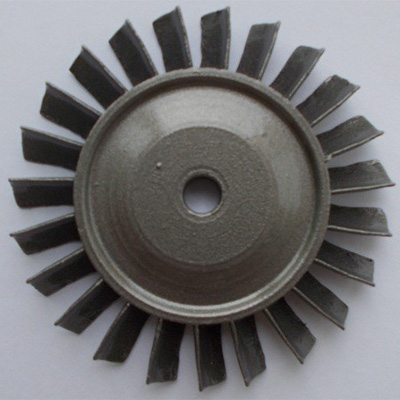
Key external to the university beneficiaries of the strategic academic unit activities
Customers of R&D: United Engine Corporation, JSC "Kuznetsov", Central Institute of Aviation Motors named after Baranova, JSC "RCC" Progress, Khrunichev State Research and Production Space Center, "Bryansk Engineering Plant, JSC" Aircraft Engine "RSC" Energia ", JSC" Metallist ".
Consumers of staff: United Engine Corporation and aerospace cluster of Samara region.
Partners in joint training: JSC "Kuznetsov" (Samara), JSC "Metallist", University of Stuttgart (Germany), University Polito (Italy);
Partners R&D: Central Institute of Aviation Motors named after Baranova, All-Russian Research Institute of Aviation Materials, Experimental Design Bureau. A. Lyulka (branch of JSC Ufa Engine Industrial Association) (Moscow), OSC “Konstruktorskoe Buro Khimavtomatiky” (Voronezh), Institute of Mechanical Engineering named after A.A Blagonravova of the Russian Academy of Sciences ", JSC Scientific and Production Assotiation "Concern "Aurora", OAO Gazprom, the company of GE (Baden, Switzerland), University of Stuttgart (Germany), Polito University (Italy), the firm" Price Induction "(Biarrits, France), China University of petroleum (Beijing, China), etc.
Resource base of the strategic academic unit
The complex of technological equipment for mechanical processing:
milling machining center MicronUCP 800 Duro; milling machining center MicronUCP 600 Vario; milling machining center Sterlitamak S500L; turning and milling center Traub TNA 300; CNC milling machine Alzmetall BAZ; electro-discharge drilling machine AGIE CHARMILLES MIKRON; wire electrical discharge machine GF AGIE CHARMILLES; Grinding and sharpening CNC Center VIZAS VZ-630F4; coordinate measuring machine DEA GLOBAL PERFORMANCE 0710.07; an automated system for the determination of residual stresses on the base unit ACB-1.
The complex of technological equipment for laser processing: laser unit HTS-300; laser laboratory on the basis of a gas laser ROFIN DCx10; installation for welding on the basis of solid-state laser ROFIN StarWeld; Specialized unit for welding on the basis of solid-state laser SWMP.
The complex of imaging of vibro-acoustic aviation and space-rocket object fields LMS SCADAS Mobile with expanded configuration.
The complex of vibro-acoustic monitoring and diagnostics of aviation and space technology-based on 3-component scanning vibrometer PSV-400-3D with expanded configuration manufactured by Polytec (Germany).
The complex of additive technologies laboratory equipment: 3D printer. EDEN 350; installation of metal powder selective laser melting SLM 280HL with laser power 400 W; system for vacuum polymers casting 4/05 MTT; system for vacuum stainless steels casting SGA 3500.
Technological complex for manufacturing composite acoustic complex surface fillers of resonant type sound-absorbing structures, including the three component portable laser vibrometer, test kit based on dual reverberation chamber for the study of acoustic characteristics of sound-absorbing structures, acoustic camera Nor848.
The complex of equipment for the study of the working processes in the GTE: Laser Doppler measurement system for 3D diagnostics of gas-liquid flows; educational and measuring complex of automated gas-dynamic research; optical system of phase Doppler measurements of flow parameters 3D PDA; educational and research equipment complex for analyze microflow structure; educational and research equipment complex for research flame structure by PLIF; three-component semiconductor laser Doppler anemometer to measure the particle size for the diagnosis of gas-liquid flows LAD-0789S-PDA; 3D thermo-anemometer for measuring the reference speed and turbulence flows.
Bench-testing unit: test bench for small-sized jet-prop engines; test bench for testing small-size turbojet engines; climatic test bench; test bench with AI-25 turbofan engines.
Center for aircraft engines history, having more than 70 full-scale mockup of prepared aircraft engines.
Complex of the test equipment: vibration system TIRA TV model 59335/RIT-340; pull test machine QUASAR 25; climatic test chamber, cold-water heat KTHV 100/70-260; shock table Lansmont model 152; universal servo-hydraulic testing machine Instron Model 8802, 250kN; noncontact measurement system ARAMIS HS.
Equipment for the testing of engine guidance system units.
The information base for engines, contain a description of engines, 110 2D-models and 10 3D-models of engines, educational materials for the engine study and design.
Organizations which are interested in collaboration with the strategic academic unit
Established in IDEU design and technological training and prospects of its development are of great interest both from domestic and foreign organizations and enterprises. Among domestic enterprises should be noted of JSC "Kuznetsov", JSC "Metallist", JSC "Aircraft Engine", NPO "Saturn", among foreign - SNECMA (France), technical universities Stuttgart and Turin, is negotiating with the universities of France and Canada.
Our graduates have great scientific and technical potential and quickly moving up the career ladder. There are examples when graduates within three years reached the position: Head of department (JSC "Kuznetsov"), head of the strength department (JSC "Kuznetsov"), Chief Designer (JSC NPO "Saturn"). JSC "Kuznetsov" is financing 50% of the cost of training technologists, the educational program "Technology of engines production" (bachelor). JSC Moscow Engineering Enterprise named after V.V Chernyshev has decided to finance the master's educational program "Design and technology of manufacturing gas turbine engines".
Double degree program developed in conjunction with the technical universities of Turin (Italy) and Stuttgart (Germany), engineering training and Laappeentranta (Finland) - training in mechatronics.
The two-month engineering training program of bachelors (Summer School) was organized with the Technical University of Stuttgart. In 2015, the first 10 people group of German students successfully completed training program. Classes were given in English.
Decision was made to the annual organization of a summer school for 25 ... 50 German bachelors. SSAU is included Technical University of Turin in the proposal to create a consortium of European universities for the training of masters in the field of dynamics and strength engine.
taking part in StrAU
Seven departments: “Automatic Systems of Power Plant”, “Engineering drawing”, “Construction and Design of Aircraft Engines”, “Aircraft Engines Theory”, “Thermal engineering and heat engines”, “Engine Production Technology”, “Ecology and life safety”.
Two institutes: “Innovative Production Technologies Institute”, “Machines Acoustics Science and Research Institute”.
Nine research laboratories: “Aeronautical Products Vibration Strength and Reliability Industrial Research Laboratory”, “Mechanical and Spot Blasting Materials Treatment Industrial Research Laboratory”, “Manufacturing Processes Automation Technologies Industrial Research laboratory”, “Laboratory of additive technologies”, “Laboratory of energy-efficient and energy-saving technologies”, “Jet Engine Workflows laboratory”, “Rapid prototyping laboratory”, ‘Thermal Power Engineering laboratory’.
Six scientific and educational centers: “Vibroacoustics of Machines”, “Laser systems and technologies”, “Mechatronic Systems and Robotic Complexes”, “Gas-dynamics research”, “Energy efficiency”, “Prototyping”.
Two multiple access centers: “Interdepartmental Training Research and Production Center СAM-technology”, Teaching and Research Production Center Vibration strength and reliability of aerospace parts”.
Three joint scientific subdivisions in cooperation with foreign universities and companies: Russian-German “Advanced engines research institute” (with University of Stuttgart, Germany); Scientific laboratory “Gas-turbine engines rotor dynamics” (with Polytechnic University of Turin, Turin, Italy); Russian-German Scientific laboratory “Tensometry and telemetry” (with MT – Solutions company, Germany); production and technological laboratory "Fundamental research and innovation technology".
Other departments: “Student Design Bureau of aircraft engines”, “Center for History of aircraft engines”.
Educational programs, implemented in StrAU
Direction 13.03.03 “Power engineering”: bachelor’s degree program “Accessory and power plants control systems” with the number of students – 84 people;
Direction 15.03.04 “Automation of technological processes and production”: bachelor’s degree program “Mechatronic and robotic systems” with the number of students – 71 people;
Direction 15.03.05 “Design and technological support of machine-building manufacture” of bachelor’s degree programs:
- “Innovative production technology” with the number of students – 73 people;
- “Engine manufacturing technology” – personnel contract training for JSC “KUZNETSOV” with the number of students – 75 people;
Education of students at JSC “KUZNETSOV” was organized in 2000 to effectively solve stuffing problems of the leading aerospace company. A unique system of training and manufacturing processes integration was developed. Students work and study in the factory and perform laboratory works at the university. Coursework and thesis are carried out on topics, which are formed in the factory departments under the joint leaderships of a university teacher and a specialist from JSC “KUZNETSOV”.
Direction 24.03.05 “Aircraft engines” of bachelor’s degree programs:
- “Design of aircraft engines and power plants” with the number of students – 44 people. Russian partners: JSC “KUZNETSOV”, JSC “Metallist”. Their roles are: coordination of curricula, formation of actual topics of the coursework and thesis, students consulting by coursework performing, participation in a defense of the coursework or thesis, realization of industrial practices.
- “Organization and manufacturing management” with the number of students – 53 people.
Specialty 24.05.02 “Design of aircraft and rocket engines”: specialist program “Project management and integrated information technology in aero-engine manufacturing” with the number of students – 71 people. Russian partners: JSC “KUZNETSOV”, JSC “NPO “Saturn”. JSC “Metallist”. Their roles are: coordination of curricula, formation of actual topics of the coursework and thesis, students consulting by coursework performing, thesis guidance, participation in a defense of the coursework or thesis, realization of industrial practices, assignments development for the contract training and active participation in it.
Direction “Aircraft engines” of master’s degree programs:
- “Hi-tech innovative machine-building manufacture” with the number of students – 18 people;
- “Mechatronic pneumohydraulic accessories and systems” with the number of students – 11 people;
- “Integrated information technology in aero-engine manufacturing” with the number of students – 2 people. Russian partners: JSC “KUZNETSOV”, JSC “Metallist”. Their roles are: coordination of curricula, formulation of actual topics of scientific works, students consulting, equipment provision for the experimental work, participation in scientific work defenses, realization of industrial practices.
- “Power plants and energy systems of aircrafts” with the number of students – 1 person. The main partner – Stuttgart University (Germany). The training is carried out in the form of the integrated Russian-German education. 1st year students study at the home university. 2nd year students have an opportunity to study at the partner university to obtain a double diploma. There is also a possibility of students exchange for a semester.
Post-graduate programs (94 people):
05.07.05 Heat and electric rocket engines and power plants of aircrafts; 1.02.06 Dynamics, strength of machines, devices and equipment; 05.07.07 Control and testing of aircrafts and their systems; 24.06.01 Aeronautical and rocket space engineering”; 05.02.22 Manufacturing process management.
Examples of successful career development of graduates
Efimov E.V. has gone the way from the engineer to the chief designer after three years of working in the NPO Saturn Company; Selivanov I.A. has become the head of the strength department after two years in design bureau of JSC “Kuznetsov” Company; Tsygankov I.V. has become the head of the regional division after two years of working in "Kelvion Mashimpeks" (Germany); Zhdanov I.A. and Sokolov M.V. after graduation enrolled in a Doctoral program of the University of Stuttgart (Germany); Klusachek M. has become a leading specialist of the turbocharged division after three years of working in the Scientific and Technical Center of the BOSCH Company (Shtutgart, Germany); Sergeev D.V. – Deputy director of the factory; Ivanova OA - Deputy Head of department of JSC "Russian Railways"; Korchagin I.O. and Valuev S.T. - Department heads of JSC “Kuznetsov” Company; Zhukov D.S. - Deputy head of the department of "Metallist-Samara" Company; Evgeny Suslin, Head of Center of Excellence, ALCOA Artem Korotygin, Project Manager for Polymeric Composite, JSC "NPO "Saturn" and many others.
Main completed StrAU projects in the past three years
1. Integrated project of creation the high-tech manufacturing "Creation of effective design technologies and high-tech manufacturing of high-power gas turbine engines for the ground power plants”. Project Manager – Alexander Ermakov, Director of Aerospace Propulsion Institute SSAU, was born in 1951. Industrial partner – JSC "Kuznetsov". contract value is 190 million rubles.
The original technical solutions for the main engine components have been developed and implemented, reasonable geometric dimensions which provide required reliability and effectiveness of the modified and uprated engines have been chosen by performing the simulations and experiments. As a result of work upgraded compressor has been designed. The optimization of the low pressure turbine and free power turbine workflows was performed considering the mutual influence of turbines, enabling improved efficiency of the turbines. As a result of the works air brake PT-36-32 (32 MW) has been designed with a wide application "virtual" testing technology in the design process, implemented in the software package NUMECA FineTurbo. A technical proposal on the final version of the intermediate-pressure compressor support design with a modified number and shape of racks was found in order to radically reduce the amplitude of dangerous harmonics acting on the impeller of the fifth compressor stage. This proposal has been obtained as the result of the complex "virtual" gas-dynamic and strength tests.
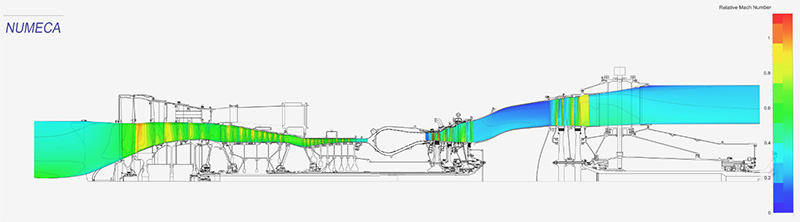
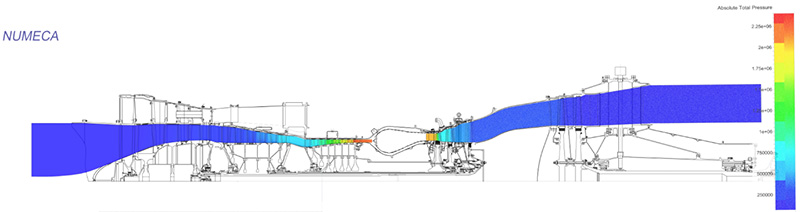
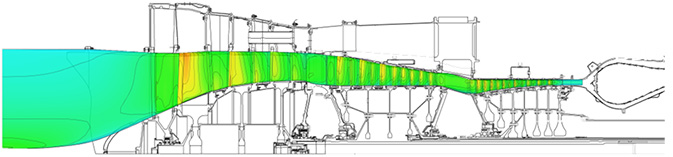
Developed and implemented radial-face seals with hydrodynamic and hydrodynamic lubrication, elasto-damping piping supports, vibration isolators made of Metal-Rubber (MR) material. Upgraded unit APM-25, allowing to reduce influence of the steering system units of gas-dynamic stability of compressor and combustion processes in the combustion chamber of the engine NK-36SТ. Developed computerized complex devices for bench control angular and linear displacement element rotating units of gas-turbine engines, namely, measuring the dynamic changes of radial clearances and profile end section of fan blade (PRIZ-1) and measuring a dynamic displacement element (ILDP-8) angular contact bearing high-pressure compressor. It has been created burner for the combustion chamber of the engine NK-36SТ with increased to 32 MW capacity, developed two versions of unified combustion chamber of the engine NK-36SТ, the study of the burner in the experimental tests allowing to choose the best mode of its work with good parameters of emission of Nox and CO.
Produced the experimental technological process of the modified low pressure compressor gas generator (NK-36) rotor blades, developed a set of measures to improve the accuracy control of geometrical parameters of blades and their castles, including during the treatment. Received a wax model of the compressor stator blades and transferred to JSC "Kuznetsov" for the production of castings with directional crystallization. It has been developed The technology of selective laser sintering bladed swirler for the gas turbine engine. As a collaborator in this project has been Russian Research Institute of Aviation Materials. They have done testing of obtaining parts made of alloy VTI-4 and alloy VJL21, which are not inferior to the properties of the alloys-analogues made in the USA.
2. The agreement with the Institute of Biomedical Problems, Russian Academy of Sciences to create a simulator vibration isolation systems for the International Space Station (ISS) together with a stand for the training of astronauts on the ground with simulated space conditions. In April 2015 the space cargo ship "Progress" delivered to the ISS treadmill for Russian cosmonauts to the vibration isolation system, designed and manufactured in Samara State Aerospace University, which allowed the US to remove the track from the Russian segment of the station and in it to date, all domestic production of simulators;
Project Manager - Alexander Ermakov, Director of the Institute of engines and power plants SSAU, born in 1951. The amount of the contract - 10 million rubles.
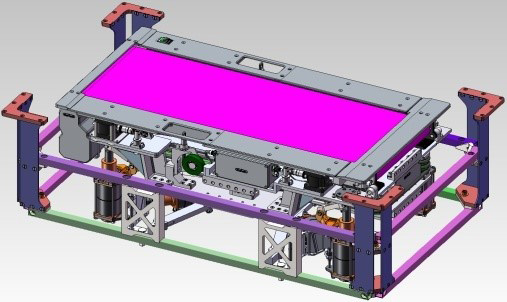
3D model of the simulator "Treadmill" with vibration isolation system
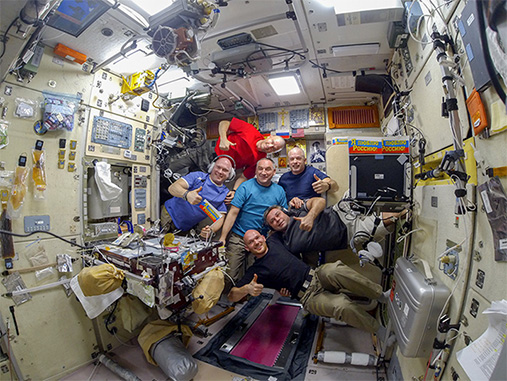
Simulator "Treadmill" on the ISS
3. The agreement with the Federal State Autonomous Educational Institution of Higher Education "Saint Petersburg State Polytechnic University" "Creating parts and aircraft engine components production high-technology methods of heterophase powder metallurgy." .
Project Manager - Sergey Murzin Professor. The amount of the contract - 10.47 million rubles. The results of the research project is a development of technological head shape for the technology implementation of direct laser growing complex-dimensional products from powder alloys; technological development of recommendations for the restoration of worn and / or damaged geometry of metal and aircraft engine production by direct laser deposition.
4. The agreement with JSC "CIC CO." Project Manager - Nikolay Pronichev, deputy head of the department of aircraft engines production SSAU, born in 1950. The amount of the contract - 6.5 million rubles.
In the course of work have been mastered advanced production technology, can reduce the time and improve the quality of R & D, especially at the stage of prototyping and variant studies. Thus, it became possible to provide the Samara region plant, the maximum access to modern engineering and manufacturing complex, integrated environment "design, pre-production, experimental production" in order to improve the quality and competitiveness of products produced by industry in the region.
5. The agreement with with JSC "Kuznetsov" on the preparation of serial production of a number of parts of the engine NK-33. Project Manager - Nikolay Pronichev, deputy head of the department of aircraft engines production SSAU, born in 1950 The amount of the contract - 12 million rubles. Due to the contract for three years innovative manufacturing techniques for unique rocket engine parts have been worked out. It has been done obtaining billets of special parts on the basis of rapid prototyping methods, magnetic-pulse pressing copper jacket cooling of combustion chamber, getting with a complex profile parts made of sheet materials for special blanks by hot volume stamping, drawing special thermal barrier coatings on the surface of the rocket engine combustion chamber.
There is a under development of small gas turbine engine in Institute of engines and power plants SSAU. There are a number of designs developed using a "virtual analog" technology, mastered the technology of important engine parts production.
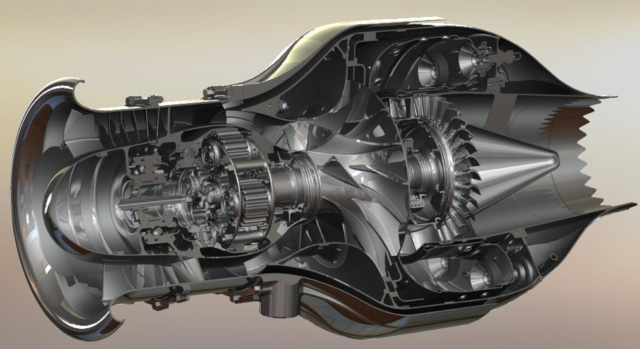
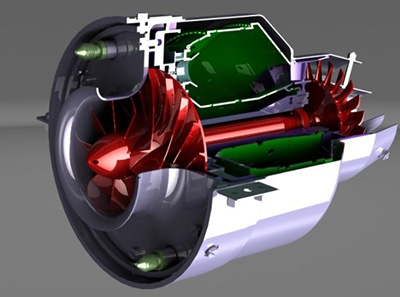
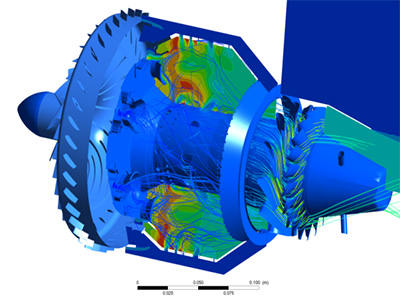
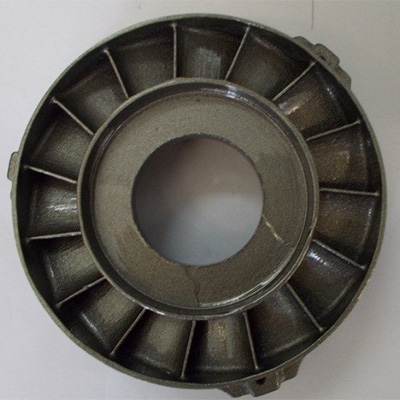
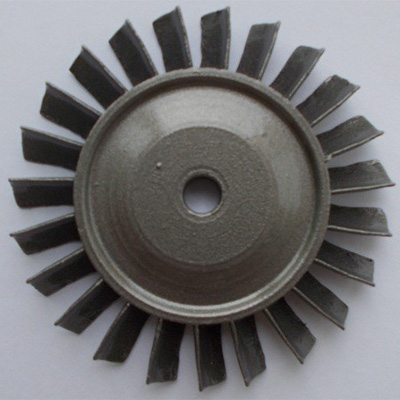
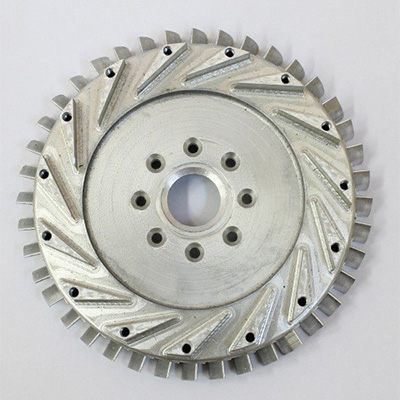
Key external to the university beneficiaries of the strategic academic unit activities
Customers of R&D: United Engine Corporation, JSC "Kuznetsov", Central Institute of Aviation Motors named after Baranova, JSC "RCC" Progress, Khrunichev State Research and Production Space Center, "Bryansk Engineering Plant, JSC" Aircraft Engine "RSC" Energia ", JSC" Metallist ".
Consumers of staff: United Engine Corporation and aerospace cluster of Samara region.
Partners in joint training: JSC "Kuznetsov" (Samara), JSC "Metallist", University of Stuttgart (Germany), University Polito (Italy);
Partners R&D: Central Institute of Aviation Motors named after Baranova, All-Russian Research Institute of Aviation Materials, Experimental Design Bureau. A. Lyulka (branch of JSC Ufa Engine Industrial Association) (Moscow), OSC “Konstruktorskoe Buro Khimavtomatiky” (Voronezh), Institute of Mechanical Engineering named after A.A Blagonravova of the Russian Academy of Sciences ", JSC Scientific and Production Assotiation "Concern "Aurora", OAO Gazprom, the company of GE (Baden, Switzerland), University of Stuttgart (Germany), Polito University (Italy), the firm" Price Induction "(Biarrits, France), China University of petroleum (Beijing, China), etc.
Resource base of the strategic academic unit
The complex of technological equipment for mechanical processing:
milling machining center MicronUCP 800 Duro; milling machining center MicronUCP 600 Vario; milling machining center Sterlitamak S500L; turning and milling center Traub TNA 300; CNC milling machine Alzmetall BAZ; electro-discharge drilling machine AGIE CHARMILLES MIKRON; wire electrical discharge machine GF AGIE CHARMILLES; Grinding and sharpening CNC Center VIZAS VZ-630F4; coordinate measuring machine DEA GLOBAL PERFORMANCE 0710.07; an automated system for the determination of residual stresses on the base unit ACB-1.
The complex of technological equipment for laser processing: laser unit HTS-300; laser laboratory on the basis of a gas laser ROFIN DCx10; installation for welding on the basis of solid-state laser ROFIN StarWeld; Specialized unit for welding on the basis of solid-state laser SWMP.
The complex of imaging of vibro-acoustic aviation and space-rocket object fields LMS SCADAS Mobile with expanded configuration.
The complex of vibro-acoustic monitoring and diagnostics of aviation and space technology-based on 3-component scanning vibrometer PSV-400-3D with expanded configuration manufactured by Polytec (Germany).
The complex of additive technologies laboratory equipment: 3D printer. EDEN 350; installation of metal powder selective laser melting SLM 280HL with laser power 400 W; system for vacuum polymers casting 4/05 MTT; system for vacuum stainless steels casting SGA 3500.
Technological complex for manufacturing composite acoustic complex surface fillers of resonant type sound-absorbing structures, including the three component portable laser vibrometer, test kit based on dual reverberation chamber for the study of acoustic characteristics of sound-absorbing structures, acoustic camera Nor848.
The complex of equipment for the study of the working processes in the GTE: Laser Doppler measurement system for 3D diagnostics of gas-liquid flows; educational and measuring complex of automated gas-dynamic research; optical system of phase Doppler measurements of flow parameters 3D PDA; educational and research equipment complex for analyze microflow structure; educational and research equipment complex for research flame structure by PLIF; three-component semiconductor laser Doppler anemometer to measure the particle size for the diagnosis of gas-liquid flows LAD-0789S-PDA; 3D thermo-anemometer for measuring the reference speed and turbulence flows.
Bench-testing unit: test bench for small-sized jet-prop engines; test bench for testing small-size turbojet engines; climatic test bench; test bench with AI-25 turbofan engines.
Center for aircraft engines history, having more than 70 full-scale mockup of prepared aircraft engines.
Complex of the test equipment: vibration system TIRA TV model 59335/RIT-340; pull test machine QUASAR 25; climatic test chamber, cold-water heat KTHV 100/70-260; shock table Lansmont model 152; universal servo-hydraulic testing machine Instron Model 8802, 250kN; noncontact measurement system ARAMIS HS.
Equipment for the testing of engine guidance system units.
The information base for engines, contain a description of engines, 110 2D-models and 10 3D-models of engines, educational materials for the engine study and design.
Organizations which are interested in collaboration with the strategic academic unit
Established in IDEU design and technological training and prospects of its development are of great interest both from domestic and foreign organizations and enterprises. Among domestic enterprises should be noted of JSC "Kuznetsov", JSC "Metallist", JSC "Aircraft Engine", NPO "Saturn", among foreign - SNECMA (France), technical universities Stuttgart and Turin, is negotiating with the universities of France and Canada.
Our graduates have great scientific and technical potential and quickly moving up the career ladder. There are examples when graduates within three years reached the position: Head of department (JSC "Kuznetsov"), head of the strength department (JSC "Kuznetsov"), Chief Designer (JSC NPO "Saturn"). JSC "Kuznetsov" is financing 50% of the cost of training technologists, the educational program "Technology of engines production" (bachelor). JSC Moscow Engineering Enterprise named after V.V Chernyshev has decided to finance the master's educational program "Design and technology of manufacturing gas turbine engines".
Double degree program developed in conjunction with the technical universities of Turin (Italy) and Stuttgart (Germany), engineering training and Laappeentranta (Finland) - training in mechatronics.
The two-month engineering training program of bachelors (Summer School) was organized with the Technical University of Stuttgart. In 2015, the first 10 people group of German students successfully completed training program. Classes were given in English.
Decision was made to the annual organization of a summer school for 25 ... 50 German bachelors. SSAU is included Technical University of Turin in the proposal to create a consortium of European universities for the training of masters in the field of dynamics and strength engine.