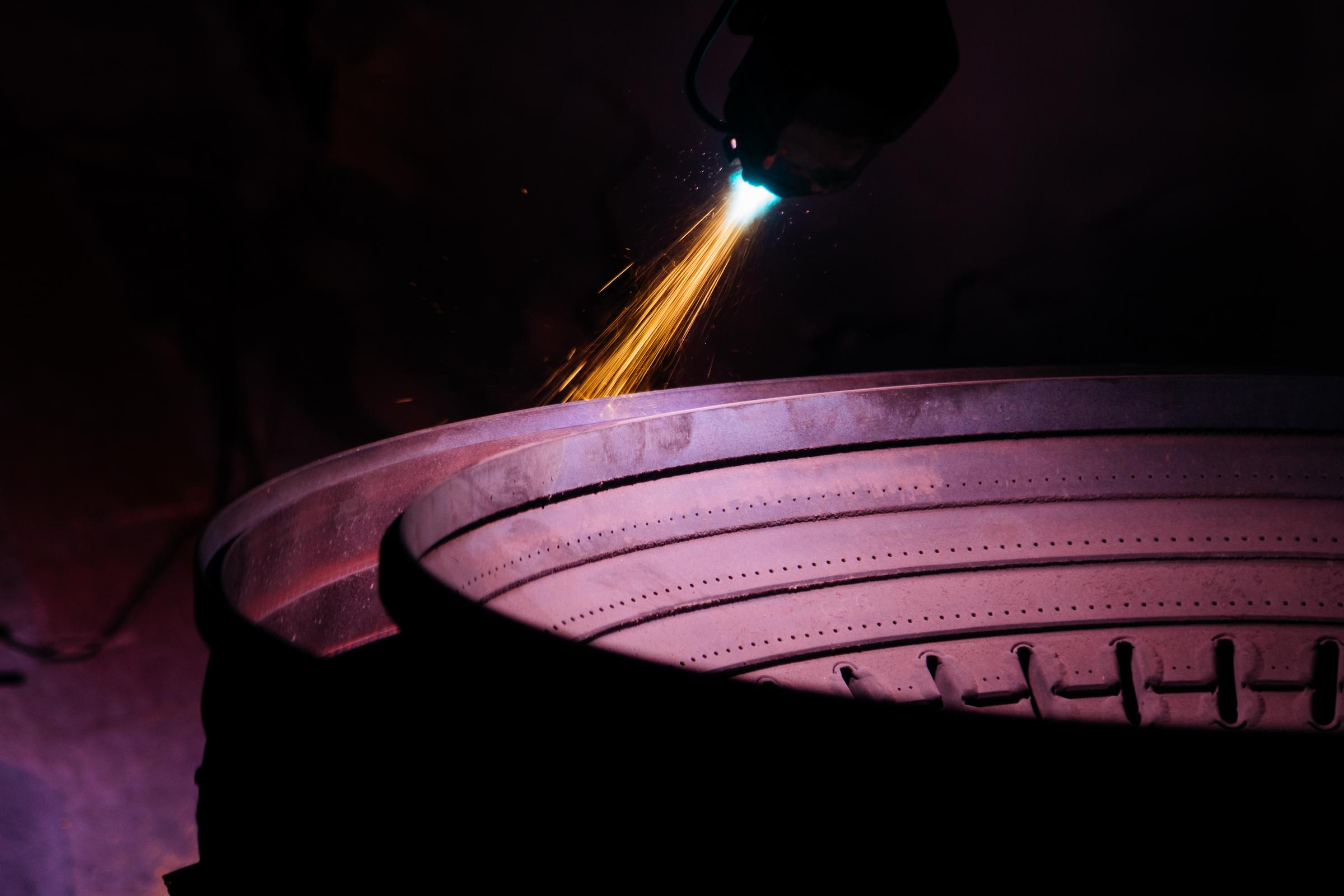
Applying this innovative technology for obtaining the coating will also make it possible for engineers to create in future more powerful engines designed for higher operating temperatures. It was being developed for two years in framework of the project, which in 2021 became the winner of the competition program “UMNIK” *, and received funding from the Innovation Promotion Fund.
“During the research, the coating technology was developed, and the first experimental prototype of the nanostructured thermal barrier coating intended for protecting engine elements from the effects of extremely high operating temperatures was manufactured. The coating is applied to the small plate made of heat-resistant material, from which the first stage blades of the turbine of a gas-turbine engine are usually manufactured. According to our calculations, implementation of this innovation will be able to increase the service life of hot section of engines by two to three times, which will accordingly increase the service life of the engines themselves”, told us the author of the project Mikhail Giorbelidze, researcher, scientific supervisor of the Research Unit of Samara University, engaged in applying special coatings.
The resulting experimental prototype currently undergoes the cycle of various tests. Thus, testing adhesion strength of the coating to the plate material have already been completed, they have shown that the strength values fully meet the requirements. According to the scientist, this coating will be able to protect from destruction internal surfaces of nozzles and combustion chambers, turbine blades and other elements of rocket and aircraft engines, gas pumping and power generating installations, as well as small-sized gas turbine engines applied in many areas, including unmanned aerial vehicles.
The coating is applied by plasma spraying: particles of a refractory substance in the form of powder, for example, zirconium dioxide with various additives, are fed into the plasma jet directed at the treated surface. Accelerating and heating up in the plasma, the particles fall on the treated item, and form the coating. The scientists have developed digital models of the process of high-speed impact of the powder-material particle, and its transformation into the crystallite ** coating; based on digital models, technological recommendations for coating modes and material preparation have been developed.
This coating is unique due to its structure: it can be compared with medieval armor – chain mail, consisting of layers of flat disc-shaped particles-scales arranged and fastened together in a special order. Thickness of one such a “scale” is 10–20 microns, and thickness of the entire “chain mail” is less than half a millimeter. Due to the developed technology, scientists managed to form two types of structure inside individual “scales”: the external special nanostructured layer increases adhesion strength of individual scales to each other and heat resistance of the “armor”. In case of fatigue crack, it will be localized by the layer within one crystallite, with no opportunity for reaching to the material of the engine part. The inner submicron layer inside the individual “scale” facilitates reduction of thermal conductivity of the material, and compensates for temperature and mechanical stresses during operation of the product at high temperatures.
“Currently, main tests for determining heat-resistant durability of the coating is underway: the experimental prototype is periodically heated to operating temperatures of the hot section of modern gas-turbine engines, followed by cooling it to ambient temperature. Especially for these tests, the university scientists have created new equipment for determining not only thermal fatigue durability, but also thermal conductivity of the coating. The tests will be completed in about six months”, noted Mikhail Giorbelidze.
For reference
* “UMNIK” (“wiseacre”) (Participant of the Youth Scientific and Innovative Competition) is the program on identifying and supporting young scientists striving for self-realization by means of innovative activities. The winners of the program receive funding in the amount of 500 thousand rubles for the period of two years, for developing the scientific and innovative project.
** Crystallite is a part of the coating structure (an individual scale) that occurs as the result of crystallization and deformation of powder particles on the surface of the product.